From rubber trees to rubber in Krabi (Thailand).
From rubber to latex.
In the timid sunshine of this summer twilight, we gradually make our way into the hinterland of this beautiful island of Krabi in southern Thailand, where tourist hotels are unfortunately becoming more numerous than ever. In the early hours of the morning, the “toy” purrs along the winding road, first asphalt, then dirt and concrete. Latex harvesting in this somewhat isolated region is a major contributor to the local economy, especially for those who have not been fortunate enough to be able to turn their land into building plots for luxury hotels. In this remote part of the country, just a few kilometers from the sea, we enter the Thai countryside.
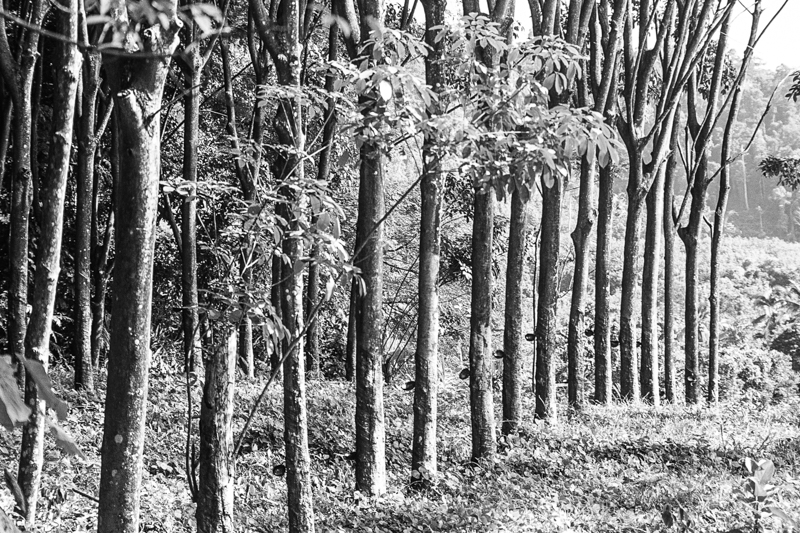
Work in the forest had been underway since 2am. As harvesting takes place in dry weather, the farmers had chosen a warm, sunny day. If the weather is too wet, the latex won’t flow well enough, so the harvest is insufficient and the quality is poor. Similarly, latex is not harvested when it rains, i.e. during the monsoon season from May to June. The plantation’s 300 trees are harvested by 10 a.m., and the latex is collected from the bottom of small sandstone pots hung just below the deep notch through which the white liquid flows drop by drop. With the iron drums for transporting the latex filled, the small team of 4 members of the immediate family head back to the farm, which for safety reasons is in the immediate vicinity of the plantation.
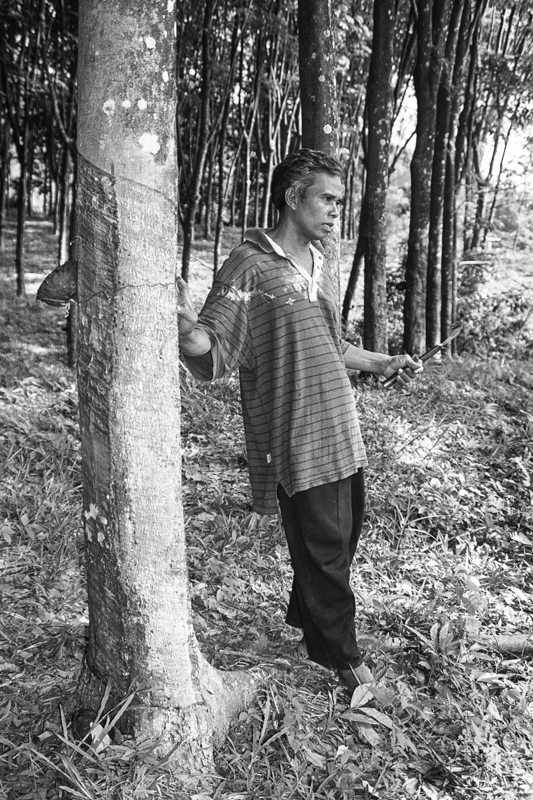
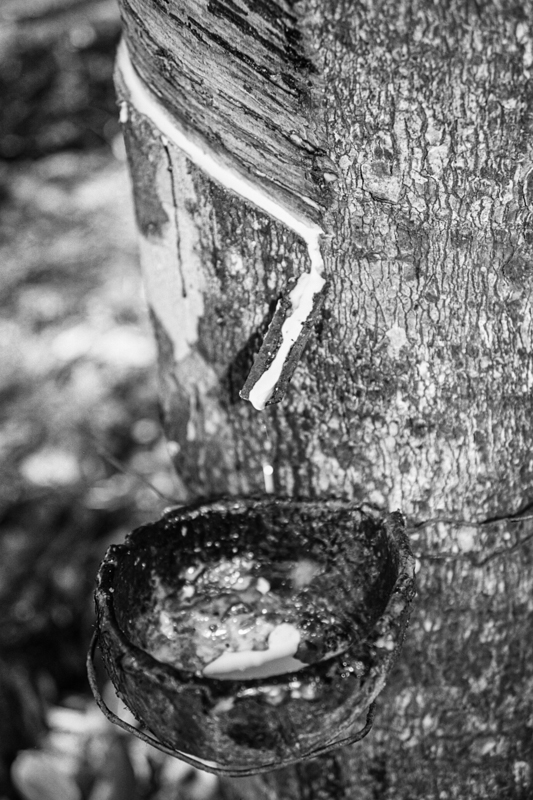
From latex to rubber…
After a few preparations and a well-deserved refreshment, the second part of the work can begin. Pure latex is mixed with water and a fast-acting polymerizer allowing the natural molecules to begin their transformation into rubber. The addition of the polymerizer is not mandatory, as latex can polymerize on its own, but it is more convenient to speed up processing so that the entire crop can be treated on the same day.
The slightly viscous mixture is then poured into rectangular tubs and skimmed . on the upper part , which consists of a foam of coagulated latex and a few impurities. This poor-quality foam rubber will be used to manufacture shoes for sale on the local market. After letting the rubber “set” for about twenty minutes, the plant manager gives the go-ahead for the duck to walk on the block thus formed on the ground on a plastic sheet to protect it from impurities.
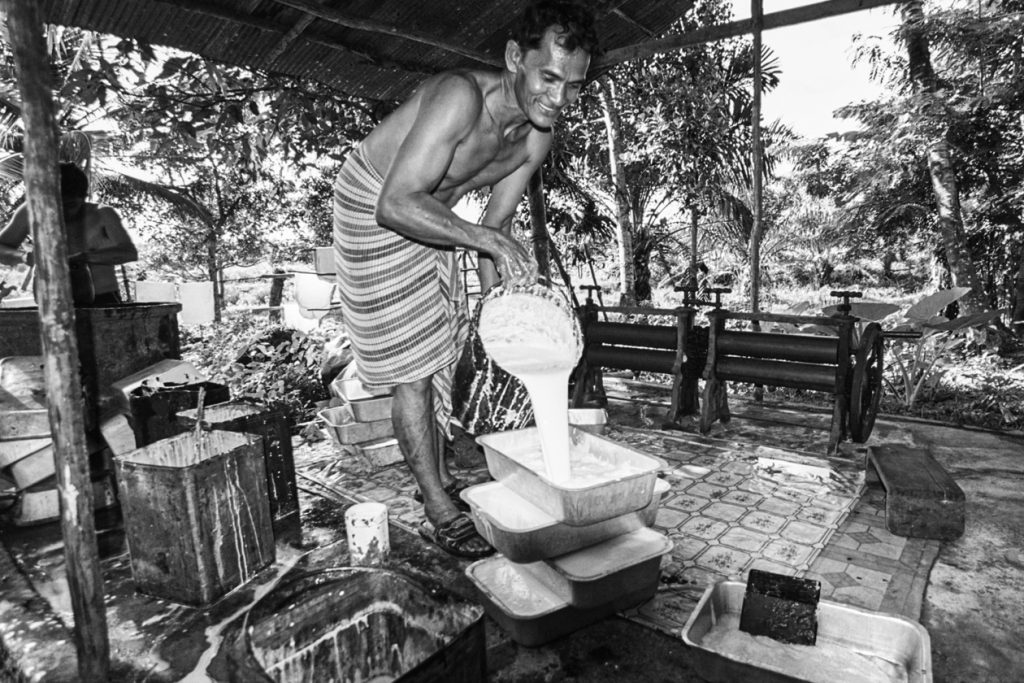
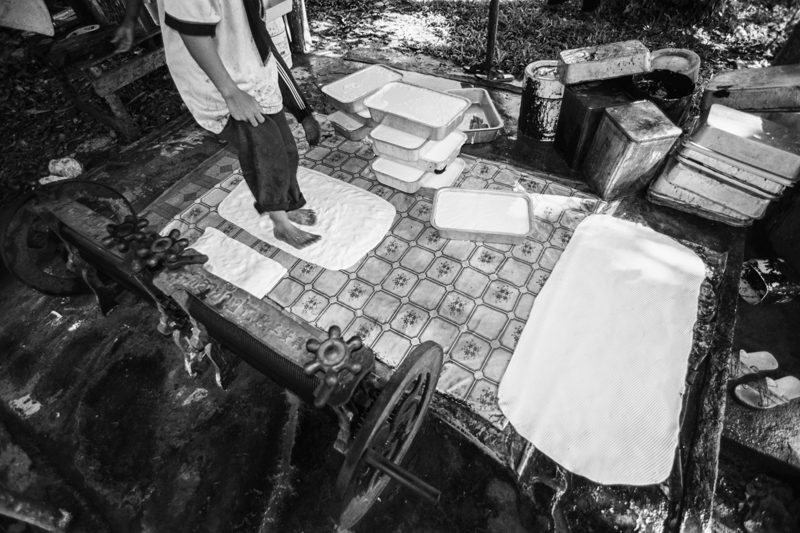
The next step is to flatten the plate into a rectangular pancake, 1 metre long and 60 cm wide. Despite the best efforts of these funny dancers, the slab is still too thick. It has to be thinned using a manual roller machine, which has a dual objective: to reduce its thickness by 2 or 3 consecutive passes through smooth rollers, and finally to imprint it with a striated pattern for faster drying. The inspected sheets are laid out in the open air to dry for around 2 days. At this stage, the rubber is still very fragile, and to complete the drying process safely and theft-proof, the sheets are locked away in a room where processing will continue for around a month. This final stage is monitored by touch to assess flexibility and thickness. Finally, the production is rolled into bales and sold for around 80 bath per kilogram, or 1.66 euros per kilogram. Despite advances in synthetic chemistry, the properties of natural rubber remain incomparable and irreplaceable for certain well-known applications such as tires, shoe soles, baby-bottle nipples and condoms, which represent only a tiny fraction of production.
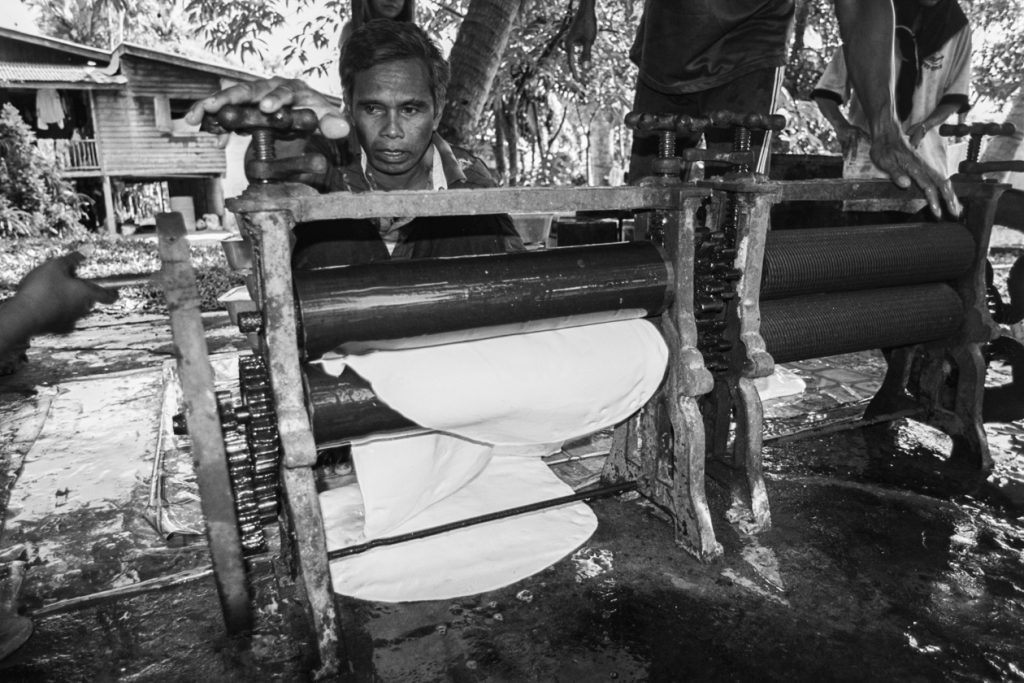

In 2004, Thailand was the world ‘s leading producer of natural rubber , with 2,866,000 tonnes out of a total world production of 8,421,000 tonnes. In 2022, total natural rubber exports are estimated at 4,27 million tonnes, an increase of 3.41% compared with 2021.
Krabi (Thailand) – September 2023